SanLucar avoids food waste by using Barcotec's smart refrigerator
SanLucar avoids food waste by using Barcotec's smart refrigerator
SanLucar, a leading international producer of fresh fruit and vegetables as well as smoothies and juices, is developing an intelligent refrigerator together with the Austrian digitalisation expert Barcotec. This ensures that convenience products can be produced fresh, promptly and in quantities in line with the market and offered to customers for purchase. Through optimised stocking, each refrigerator becomes a self-sufficient sales stand with the lowest possible spoilage.
The project received several awards: the Austrian Retail Innovation Award 2020 of the Austrian Retail Association in the category "Best In-Store Solution" , the State Award Smart Packaging 2020 in the category Digitalisation and the Top Supplier Retail Award 2021 of the EHI Retail Institute in the category Best AI & Robotics Application.
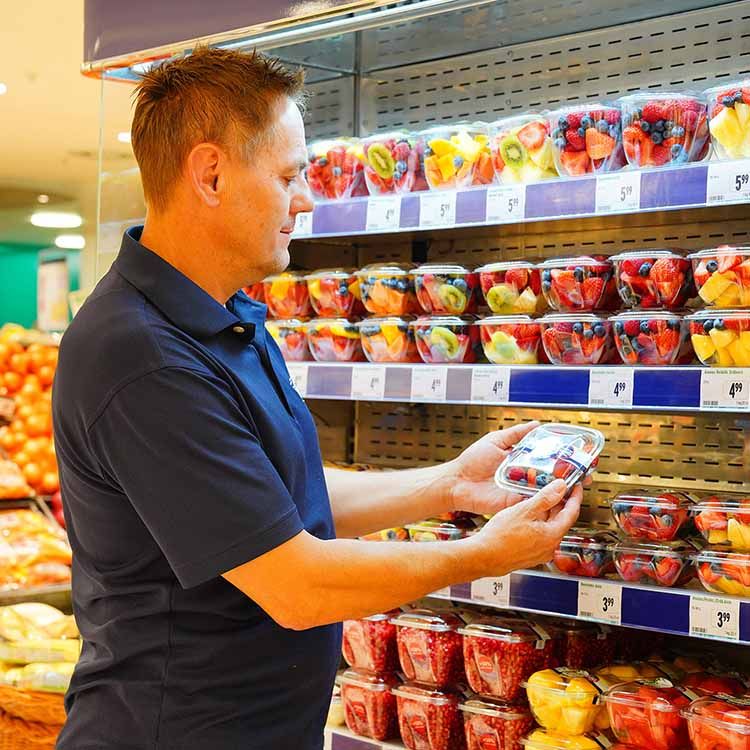
Healthy products conveniently available
The market share of convenience products (i.e. ready-to-eat products such as sliced fruit, frozen food, baking mixes, etc.) has increased more and more in recent years. Two products are particularly popular in Austria: Chilled food (pre-processed food that is ready to eat through short heating) and fresh-cut products (pre-cut fruit and vegetables), which follows the trend towards more health, wellness and organic. (Source: oesterreich-isst-informiert.at). In Austria alone, 81.94 euros per person are spent annually on convenience products. (Source: statista.com)
But the processing and production of "fresh-cut food" brings some challenges, because the goods have to be handled carefully until they reach the customer at the point of sale. Not only has fruit, for example, lost its natural protection after cutting, it also has to be portioned, cooled, stored and packaged. The lifespan of a convenience product is therefore limited.
Avoiding food waste
This is precisely the challenge that the Managing Director of SanLucar Austria, Alexander Thaller, took on in spring 2019: "Our vision is to provide everyone with the most natural, freshest and tastiest fruit and vegetables. And to do so in such a way that we can be proud of it," he says, and: "The fact that the fruit is offered pre-processed does not change anything about this requirement. But naturally, this results in a shorter life span. So we wanted to have real-time information about the condition of our produce in the grocery store so that we avoid food waste and have as much produce on the shelf as customers want to buy at that time." With this requirement in mind, they turned their attention to possible solution providers and found the Austrian company Barcotec, in which they had already found a reliable partner in the field of mobile data capture.
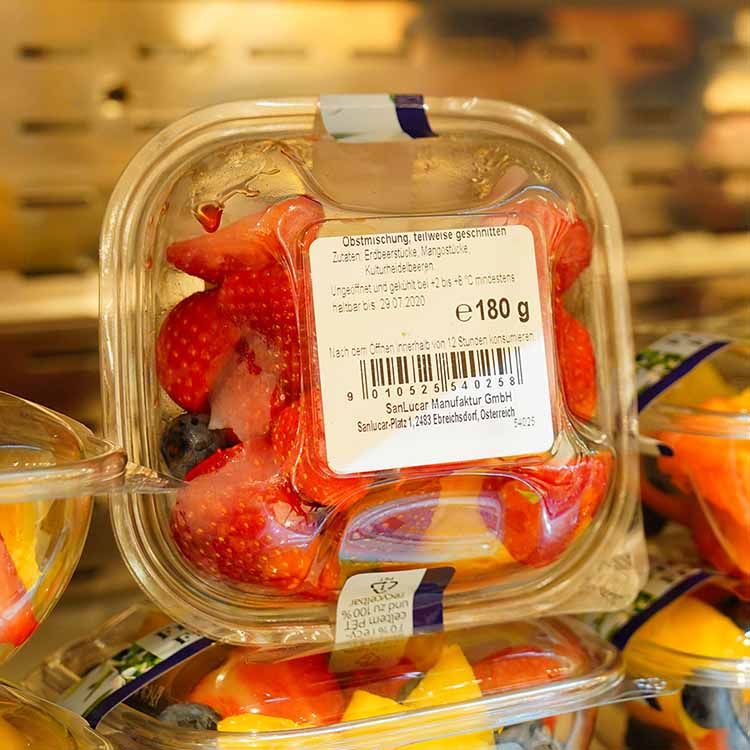
The fruit digitisation begins
Together with Barcotec, the parameters were defined that would ensure a self-sufficient refrigerator: The refrigerator was to report independently, without human interaction, when goods were inserted and removed, but at the same time continuously report the expiry data of the goods to the SanLucar head office. Special readers based on microchip technology are used to read each fruit cup. After an extensive pilot phase and months of project work, the first refrigerators were rolled out in late autumn 2019. Today, more than 100 self-sufficient refrigerators are located in food retail outlets and report their stocking level and best-before dates on their own, accurate to the second.
More freshness - less spoilage
The real-time data at the push of a button via radio chip now allow for precise production planning, as the exchange of goods is triggered in addition to out-of-shelf information. SanLucar CEO Thaller says: "Each refrigerator acts like an autonomous sales stand. For example, the fridge next to the outdoor pool can be stocked with more melons in summer when a heat wave is announced, while production is reduced when bad weather is forecast." The biggest effect is seen in greatly reduced spoilage. "It is a big concern for us to produce as little food waste as possible."
Other positive additional effects have been the reduced need for staff on the part of food retailers, as their staff no longer have to check the expiry date. For SanLucar, it is now much more transparent which varieties run particularly well on which days and when these goods are in demand in terms of time (the till receipt information is not sufficient for this). Location qualifications are now also easily possible, as it is now clear which products work well in which regions, and can thus be filled more with this product group.
Technology in a different way
At Barcotec, Regional Sales Manager Alexander Humer is responsible for the implementation of the system. He says: "The evaluation phase to select the right technology was particularly exciting. All parameters had to be right so that the goods could always be identified promptly. Our team has been working with identification technology for 30 years, but an innovative project like this required the use of absolute state-of-the-art technology."