Workshop 4.0 - STRABAG builds on digitalization
STRABAG BMTI, a subsidiary of the European technology group for construction services STRABAG SE, digitizes materials management with Barcotec.
Getting people, building materials and equipment to the right place at the right time and thus realizing complex construction projects - on time, on quality and at the best price - is STRABAG's claim. The range of services includes all areas of the construction industry and covers the entire construction value chain.
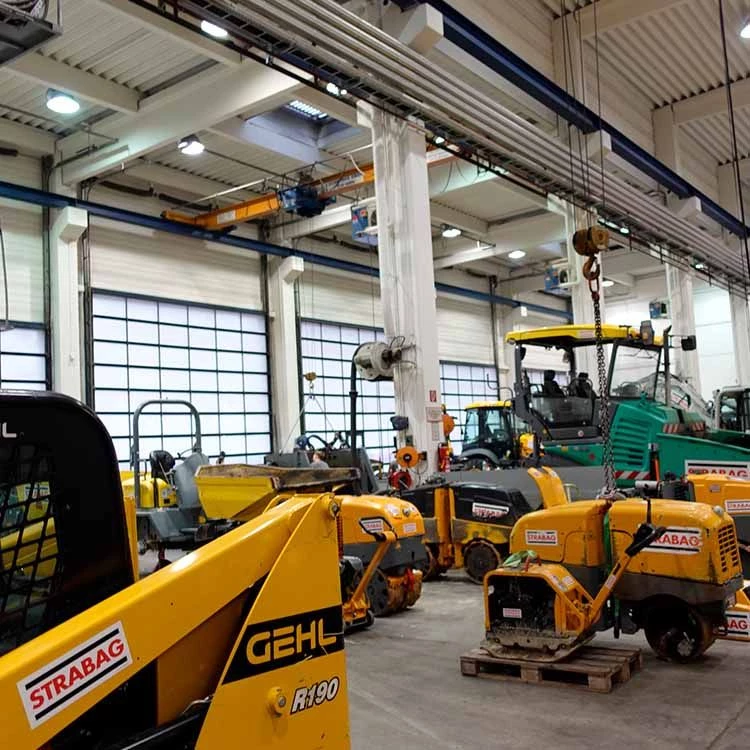
To this end, construction machinery is rented out in around 16 countries across Europe and repaired as required. The aim is to get the right equipment to the right place at the right time and in the right condition. In the warehouse of the workshops, STRABAG relies on mobile working to simplify and optimize processes. A solution was sought where mobile devices can be used directly in the existing infrastructure.
In the warehouse of the workshops, STRABAG BMTI relies on mobile working to simplify and optimize processes. In the process, a solution was sought where mobile devices can be used to work directly in the existing infrastructure.
With Barcotec, a partner for the complete solution (hardware & MDM) was found who, thanks to intensive support and consulting, takes over the turnkey shipment directly to the workshops within Europe. Michael Hofstätter, Sales at Barcotec, puts it in a nutshell: "The basis of this open and trusting cooperation is, in addition to a successful project onboarding, a customer relationship that has grown and proven itself over many years."
After two requirements workshops, the decision was made in favor of the Enterprise Mobility Management System "mCloud" from Barcotec and the Rugged Terminal BHT-1700 from Denso. The requirement was to simplify existing processes and increase efficiency - for a functioning, optimized materials management.
Thanks to the Enterprise Mobility System "mCloud", the devices used can be managed centrally. Individual default settings and user rights can also be controlled via the platform. Central roll-outs take place at the push of a button and are immediately available to the user with a simple switch-on of the device, and obstacles can be quickly resolved via remote maintenance.
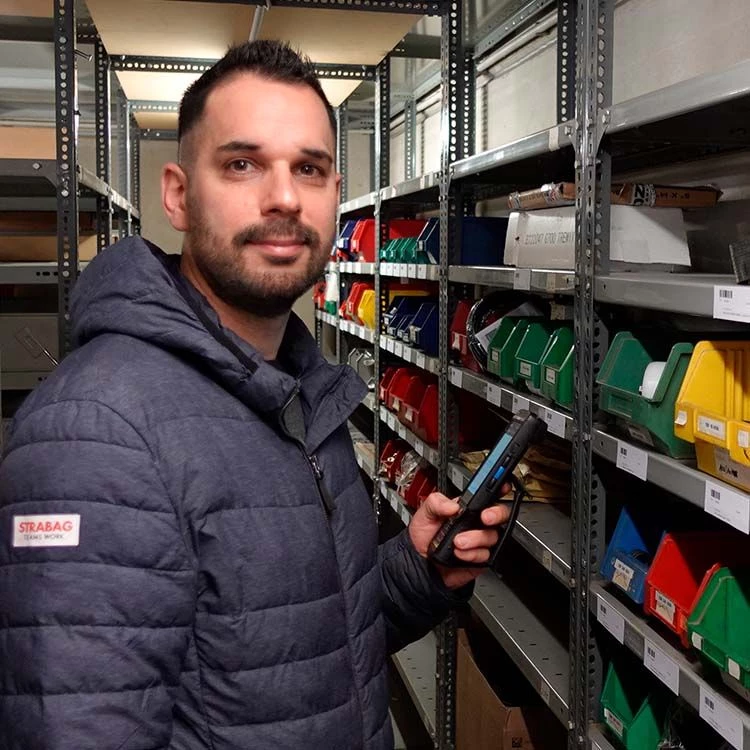
In daily use, the BHT-1700 proves to be an ideal "tool" for capturing data, as the angled scan head gives the user a clear view of the 4-inch touch display. Due to the intuitive operation of the devices, the training in the form of a short instruction was quickly completed.
A great deal of importance was attached to testing the devices in practice beforehand on both sides, so there were no unwanted surprises during implementation. But it was not only reliability, flexibility and hands-on mentality that were perceived positively by the customer - the after-sales support that Barcotec offers is also appreciated.
The resulting benefits are not only versatile, but also scalable: inventory of the warehouse was reduced from two days to just three hours.
The project manager sums up positively: "The project went according to the textbook. The requirements were clear and sufficiently formulated. Barcotec kept all promises. The change was well prepared internally, so we received very positive feedback from colleagues."